來源:江南晚報
無悔過往,無懼未來。
奮斗與機遇的交鋒,格局與視野的相逢。
數字化,是一場時代的盛會。
記者走訪多家制造業(yè)企業(yè)看到,數字化轉型已經從規(guī)上標桿企業(yè)的“可選項”,成為制造業(yè)廣泛企業(yè)的“必選項”。從錫山區(qū)獲悉,該區(qū)“智改數轉”進入快進模式,最新的三年計劃中,規(guī)上企業(yè)“智改數轉”要實現全覆蓋。如火如荼的數字化浪潮開啟時代大幕,從一個個現實案例看到,疫情期間實現逆勢發(fā)展、表現足夠韌性和抗壓能力的企業(yè),都是數字化轉型起步較早、轉型程度較高的企業(yè),這些企業(yè)從數字平臺的構建,到新消費場景的形成,及至一個個智能車間遍地開花,克服了“不敢轉”“不愿轉”“不會轉”的重重枷鎖。
案例一
傳統企業(yè)不愿轉?
宇壽醫(yī)療:從解決痛點嘗到甜頭
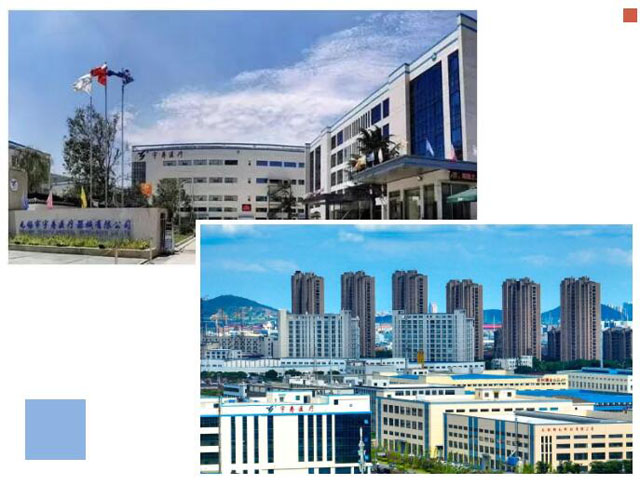
“我們生產線有個重要的工序,要把很細的金屬針頭裝到注射器上面,并進行壓力加固。因此需要大量視力特別好的員工,但頻繁的重復勞動,容易讓員工扎到自己,所以特別難招人?!?/P>
說起 2019年開始的“智改數轉”之路,宇壽醫(yī)療總經理繆李平介紹,隨著訂單量的增加,需要迅速解決產能瓶頸的“痛點”成了上馬智能化、自動化生產線的初衷。

記者在宇壽醫(yī)療看到,目前公司日常的訂單排單、生產現場以及包裝發(fā)貨,均能通過智能工廠的總控平臺“一網統管”,這個智慧中樞內,統籌整個注射器、口罩等生產線的智能化、自動化運行。除了打包發(fā)貨環(huán)節(jié)尚需相對較多人工核驗,車間內僅有少量一線員工。在其自動化改造程度最大的注射器智能生產車間,由企業(yè)定制的“??低暋笨焖贆z測系統全新上線,針對插針作業(yè)環(huán)節(jié)需要上針、上油流程的高標準安全要求,產線內置的自動拍照和識別模塊能秒速剔除不合格的產品,改變人力檢測會疲勞、會走眼等弊端。
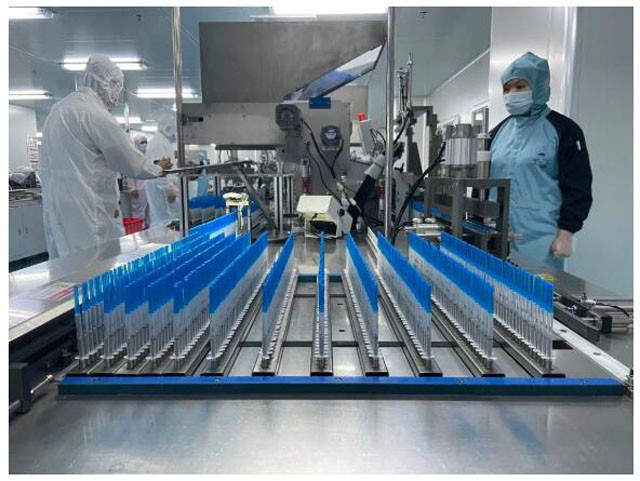
“以前最厲害的熟練工人一天能檢測1萬個針頭,而現在一套插針動作流水線上一組2人就能負責100萬支/天的產能,且產品合格率、優(yōu)品率均實現了100%?!?BR>生產現場內,穿戴防護服的工人只需關注設備運行狀態(tài),收取剔除出的殘次品即可,而實際上幾乎沒有任何殘次品出現。據悉,這套革新后的裝配生產線投用后,連工人掉根睫毛的異常都能實時檢測出。作為國內產能最大的安全式注射器生產廠家,宇壽醫(yī)療目前單日的注射器產能可達500萬支/天,實際滿產達產僅需一線員工35人。
截至目前,
今年該企業(yè)累計已經生產
1億支以上的安全式注射器,
成為當今全球產能居前列、
國內供應量最大的疫苗注射器供應商。
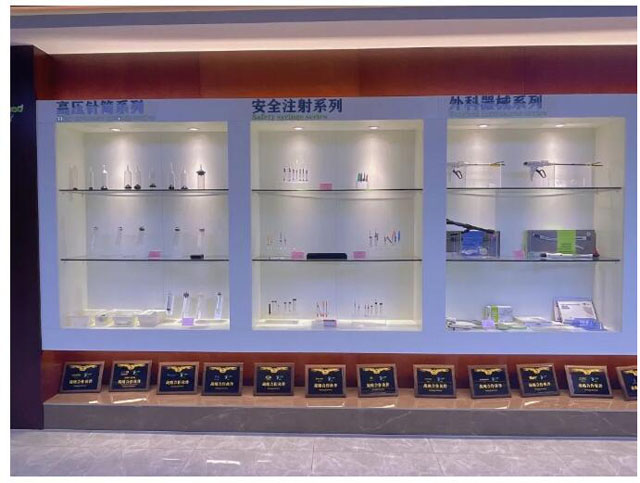
對于傳統企業(yè)來說,企業(yè)要實現生產流程的全程自動化、智能化,需要花費重資進行全新的生產路線圖設計,需要根據自己的需求和習慣重新規(guī)劃生產方式,同時也意味著整條生產線的兜底重建,一條生產線動輒數百萬元的自動化改造,“機器換人”到底值不值得?能否為企業(yè)的發(fā)展持續(xù)賦能?宇壽醫(yī)療的經驗是,值得。就在最近,這家企業(yè)獲評2022年全國第四批“專精特新”小巨人,成為國內細分領域的行業(yè)隱形冠軍?!昂茱@然,數字化讓我們實現了生產效率的升級換代,2019年開始企業(yè)陸續(xù)投入9000萬元進行數字化改造,其中用于信息采集類的數字化改造費用為1000萬元。2018年全年產出2.19億元,2021年的業(yè)績是2018年改造前的一倍,而人力減少了三分之一,當然,這個過程還能優(yōu)化進步?!?/P>
案例二
數字化扮演什么角色?
普天鐵心:轉了以后越做越高端
線上接單、線上下料、
自動生產、自動運輸,
制造業(yè)的整個生產方式
幾乎“在云端”,
一個個變壓器鐵心產品
分明又很“接地氣”。
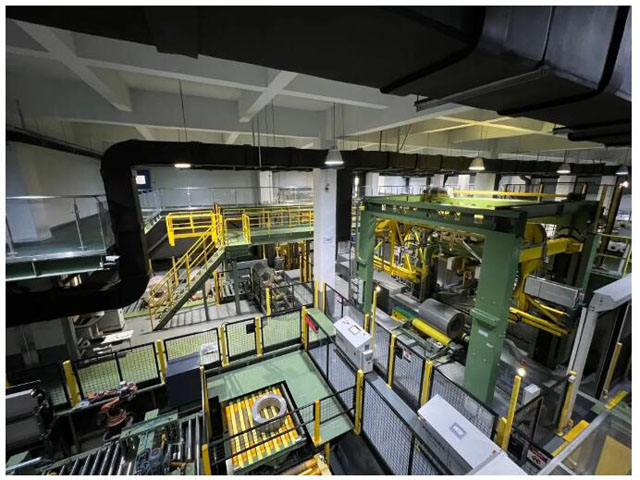
普天鐵心今年被工信部評為標桿企業(yè)數字化工廠。從一家只有十幾名工人的模仿式作業(yè)小作坊開始,位于錫山區(qū)錫北鎮(zhèn)的“普天鐵心”經過多年的自我創(chuàng)新及生產線的迭代改造,蝶變?yōu)閲鴥热鬃儔浩鳢B鐵芯全自動智能制造工廠的新標桿。這家企業(yè)先后獲得了中國制造業(yè)隱形冠軍、江蘇省智能示范車間和智能示范工廠等榮譽,是《電力變壓器用電工鋼鐵心》國家標準的第一起草單位,在其被譽為業(yè)內“黑燈工廠”的二期智慧工廠,人均產值突破了1000萬元。
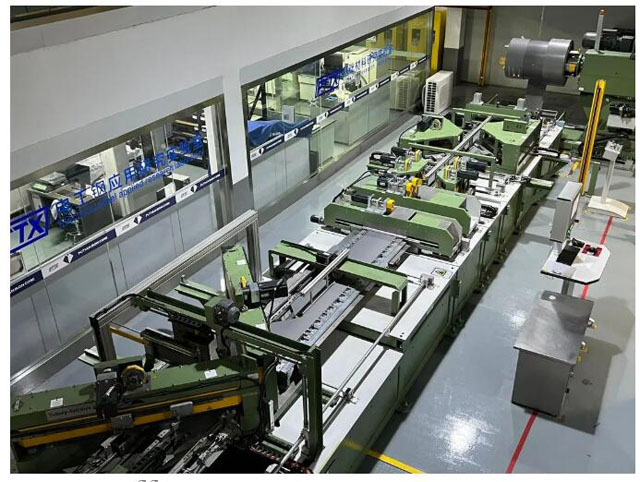
“疫情期間,全自動生產車間產能完全不受影響,管理人員即便封控在家,也能通過自主開發(fā)的綜合信息管理平臺、設備管理系統、星際物流系統等,實時獲悉、控制生產線工作狀態(tài)。”
企業(yè)副董事長梁林秋介紹,企業(yè)智能車間可智能分選并自動定時、定量配送到縱剪、橫剪及包裝設備上,整個生產、管理、供應鏈高度信息化、自動化、精益化,擁有完善的自我決策能力,在同行參觀者看來,已然是實現生產全流程自動化的“夢工廠”。
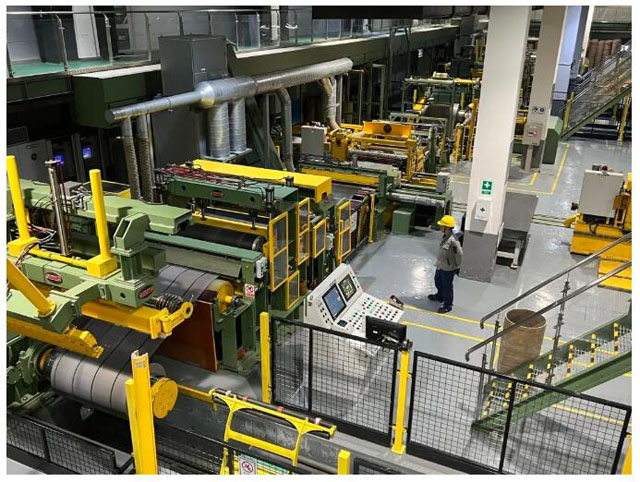
在2018年布局新建的普天鐵心二期工廠,來自瑞士的縱剪機組、德國的傳輸軌道、芬蘭的自動包裝機組,組合為同一個車間的伙伴,當系統接到訂單后瞬間生成生產指令,只見機械臂從一面重達5000噸的智能立庫墻上“抄”起一個23噸重的硅鋼卷,在縱剪機上完成大卷開小卷,接著按照薄度、規(guī)格要求將硅鋼放到作業(yè)區(qū)自主行進,然后進行剪切、套疊,實現所有生產工藝流程的最優(yōu)化。整個車間內恒溫恒濕,人與人、人與設備、設備與系統之間形成一個精密的集成互聯系統,使復雜工藝在不同工序間能夠無縫銜接。
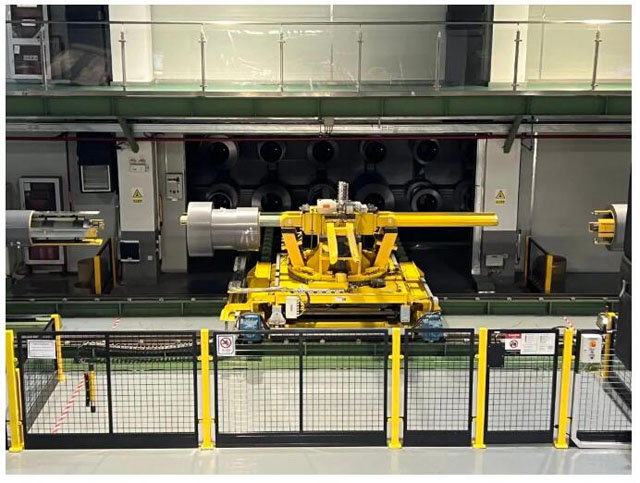
數字化在制造業(yè)究竟扮演了什么角色?
普天鐵心的答案是生產全生命周期的數據化,
從而實現系統間的深度融合。
“將運輸系統、刀具系統、生產協同系統、營銷接單系統等不同運作邏輯、不同作用的設備連接在同一個云端,形成上下游的生產順序,將采購自全球的不同機器聽從一個大腦指揮。”借助數字化,企業(yè)實現了復雜非標定制件的精細化生產,實現行業(yè)內最高標準的加工精度,且2021年單位產值能耗比2018年下降35%,2022年1—7月單位產值能耗比2018年下降58%。
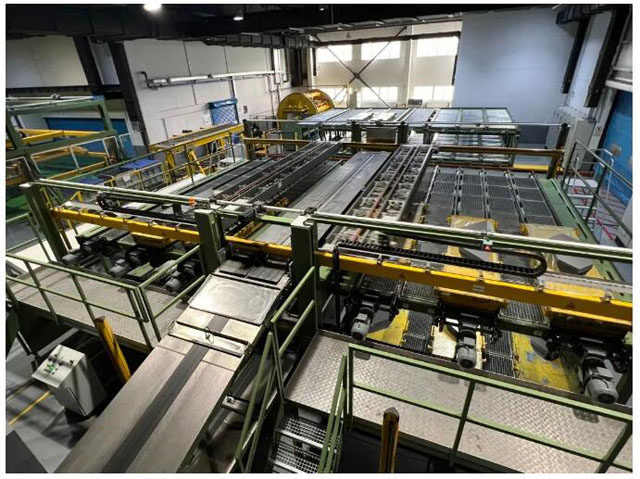
“數字化提升了企業(yè)在復雜變局下的競爭力,提高了企業(yè)產品的精度和訂單交付效率,同時更顯見的是企業(yè)應對當下以及未來的確定性?!痹阱a山區(qū)工信局負責人看來,普天鐵心的數字化之路,正從創(chuàng)新驅動的全面加速,邁向以價值為引領的高質量發(fā)展。
案例三
領先行業(yè)才能領跑賽道
紅豆工業(yè)互聯:開放平臺締造獨樂樂
到眾樂樂新生態(tài)
傳統服裝生產企業(yè)最怕什么?
庫存!
在紡織服裝生產領域深耕65年的紅豆
一直在思索為舊模式注入新活力。
2019年,
紅豆集團首次落地智能穿戴
這個新興科技領域,
摸著石頭開啟
“智能定制”的紡織業(yè)新大門。
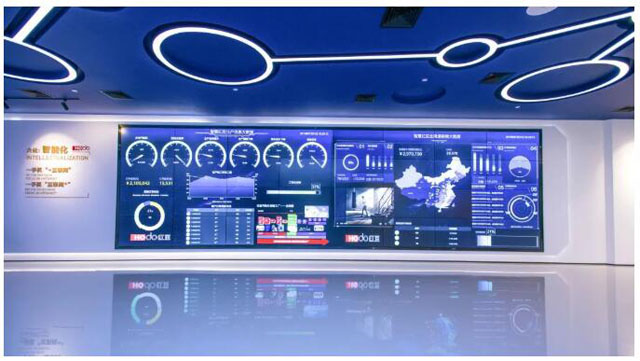
傳統的服裝生產過程是服裝公司準備面料、預測不同尺寸規(guī)格的市場份額,再進行加工生產的先生產后銷售模式,產量大意味著庫存也大的殘酷邏輯。而市場競爭激烈,產品變更頻繁,訂單趨勢越來越向多品種小批量變化,預售+生產的路徑,能最大程度減少服裝企業(yè)的“庫存”,但需要足夠敏銳快速的市場反應和快反追單能力。紅豆工業(yè)互聯是擁抱工業(yè)互聯+智能制造藍海的先行者。2019年紅豆集團宣布成立工業(yè)互聯網公司,當年12月,紅豆男裝上線“輕定制”小程序,消費者小程序上發(fā)布需求后,經過智能量體、智能打版、數據自動分發(fā),轉向平臺工廠生產、成衣配送等私人定制全過程。目前這樣的服裝定制成本并不高,一件高級襯衫三四百元,消費者可實現1分鐘量體、2分鐘出版、72小時內準備發(fā)貨,7天內全國必達的超前消費服務體驗。
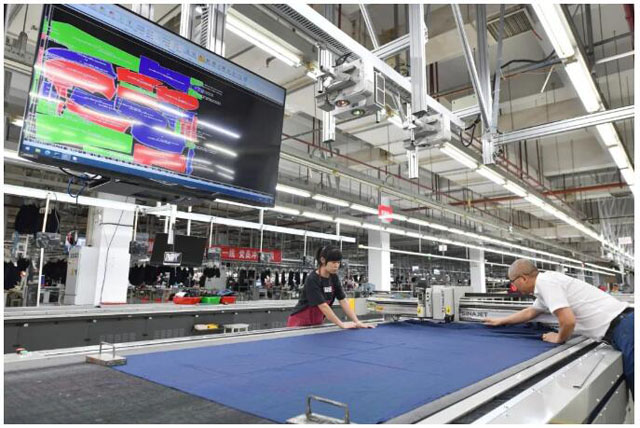
走進其中一個智能車間,每位制衣工人的工位上,都有一塊顯示屏,上面顯示每件衣服需要完成的工藝,包括每個工人當天的待完成工作量,同時對應具體的加工收入等個人工作效益。在流水線上,從前的“人找衣服”,成了“衣服找人”,自動裁床剪裁好的面料,會依次匹配給最擅長此工序的作業(yè)人員,達到在單位時間內的效能最大化。相關負責人介紹,集團內部企業(yè)打造的個性化定制+5G柔性生產智慧工廠,公司實現在制品庫存下降30%,工廠單耗成本下降10%,提高生產效率20%,實現了服裝制造鏈全過程的智能化。
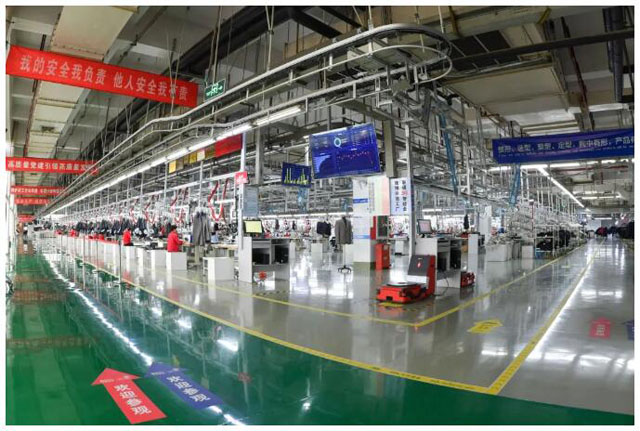
質量、成本、交期的高效協同,
進而賦予、推動整個供應鏈和
行業(yè)的技術進步、效率提升,
以及更深層次的提質增效、
整個產業(yè)鏈的協同提升。
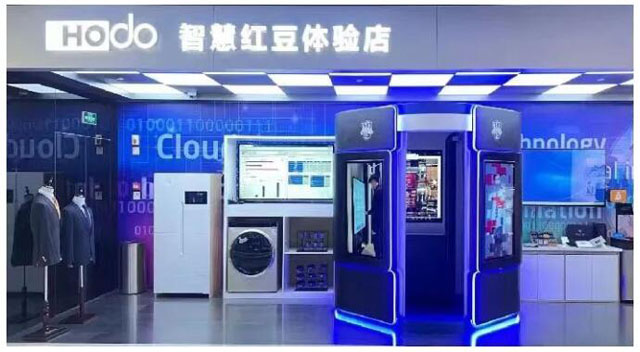
入選工信部2021年新一代信息技術與制造業(yè)融合發(fā)展試點示范項目的江蘇紅豆工業(yè)互聯實現了制造業(yè)國家“數字化”項目的突破。這個平臺,融合了紅豆居家、紅豆男裝、紅豆運動等1萬多家線下門店的消費數據集成,也上云了背后大小供應商物流、采購、銷售等現實需求的展示和進程。借助該平臺,目前已接入設備5萬臺(套),納入生態(tài)企業(yè)100家,而它采用的是免費開放給用戶和合作伙伴的模式,相關數據顯示,目前該平臺已實現交易額100億元,作為標桿型產業(yè)鏈協同生態(tài)體系解決方案,除了適用于內部300多家供應商,也向全行業(yè)10000多家企業(yè)進行推